隨著智能化技術(shù)的發(fā)展,機器視覺應用已經(jīng)深入到各個行業(yè),成為智能工廠的賦能技術(shù)。當前冶金企業(yè)也在積極探索和大力推廣機器視覺的落地應用,借助多場景的機器視覺智慧應用實現(xiàn)智能生產(chǎn)和提質(zhì)增效,加速自身向智能制造轉(zhuǎn)型。
中冶京誠數(shù)字科技(北京)有限公司結(jié)合自身在自動化控制領(lǐng)域的深厚積淀,深度挖掘制約產(chǎn)線自動化、智能化的瓶頸因素,采用深度學習、人工智能等新技術(shù),開發(fā)了機器視覺智慧感知平臺,并以此為基礎(chǔ)開發(fā)了一系列視覺應用,目前已在臨沂鋼投特鋼、昆鋼、凌鋼、鑌鑫等多家鋼企的長材車間應用場景中投入使用,通過機器視覺與基礎(chǔ)自動化深度融合,助力企業(yè)建設(shè)智能車間,提高生產(chǎn)自動化水平,降低工人勞動強度,提升生產(chǎn)效率。
邊緣端視覺感知平臺架構(gòu)
中冶京誠機器視覺智慧感知平臺基于邊緣端技術(shù)構(gòu)建機器視覺智慧應用,在現(xiàn)場應用端打造“硬件+軟件+算法”的一體化成套邊緣端機器視覺產(chǎn)品,實現(xiàn)硬件標準化、軟件模塊化和算法定制化。其中,硬件包括圖像采集設(shè)備(工業(yè)相機、安防攝像機、激光雷達、立體相機等)和存儲、計算、網(wǎng)絡(luò)等基礎(chǔ)資源,軟件包括異構(gòu)設(shè)備接入、多源數(shù)據(jù)(圖像、視頻、點云等)預處理、分析結(jié)果發(fā)布、識別控制指令下發(fā)、數(shù)據(jù)本地化等核心支持功能,算法指包括圖像處理算法、深度學習算法、點云分析算法等用于在特定業(yè)務(wù)場景下進行視覺識別的核心計算功能。平臺采用模塊化設(shè)計理念進行內(nèi)核開發(fā),支持進行應用層的二次開發(fā),定制化實現(xiàn)機器視覺在特定場景下的應用。
邊緣端機器視覺產(chǎn)品可實現(xiàn)更快的數(shù)據(jù)處理響應、計算與分析響應和網(wǎng)絡(luò)響應,滿足冶金生產(chǎn)中低延時、高響應的業(yè)務(wù)需求,同時可在較惡劣的冶金生產(chǎn)現(xiàn)場實現(xiàn)快速部署、快速調(diào)試和快速應用,大幅縮短機器視覺智慧應用的落地周期和應用成本。
不同應用場景下的邊緣端機器視覺產(chǎn)品均可接入云端服務(wù)器,視覺邊緣端的分析數(shù)據(jù)均可匯聚到服務(wù)端,支持構(gòu)建可動態(tài)擴展的全車間級智能監(jiān)控/管控應用系統(tǒng)。
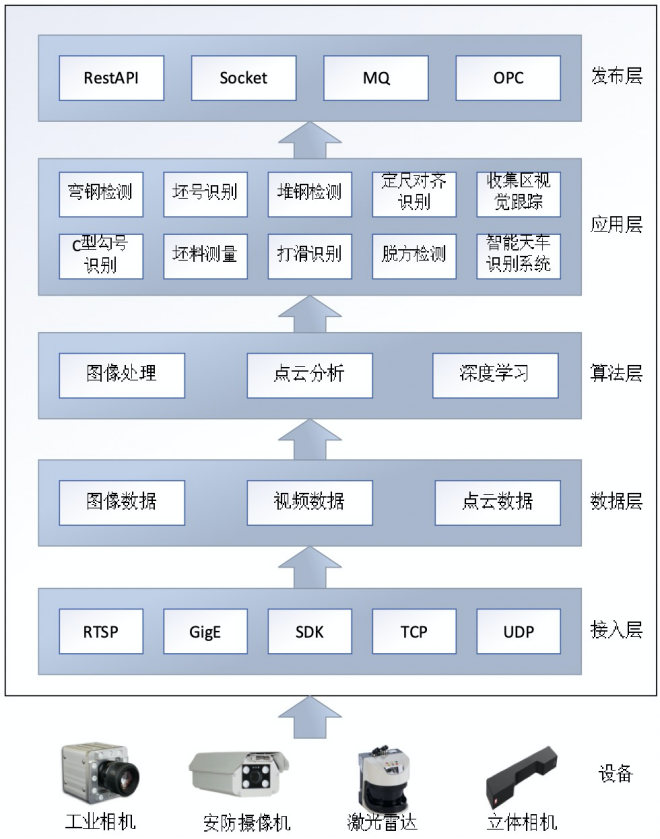
全流程、多生產(chǎn)環(huán)節(jié)應用
中冶京誠機器視覺智慧感知平臺與基礎(chǔ)自動化深度融合,實現(xiàn)坯號識別、彎鋼/脫方/測長檢測、打滑檢測、堆鋼檢測、棒材定尺擋板對齊識別、棒材收集區(qū)視覺跟蹤、C型鉤識別等功能,廣泛應用于各生產(chǎn)環(huán)節(jié),提高生產(chǎn)自動化水平,有效降低生產(chǎn)成本,節(jié)約勞動力,提高生產(chǎn)效率,降低產(chǎn)品次品率。
?。?)坯號識別
通過目標檢測、OCR字符識別算法,識別爐前輥道的鑄坯噴號字符,根據(jù)噴號識別結(jié)果,與軋制計劃進行信息核對,保證入爐坯料實物與生產(chǎn)計劃一致,實現(xiàn)了煉鋼與軋鋼信息正確真實的貫通,達到按支、根進行物料跟蹤的目的。
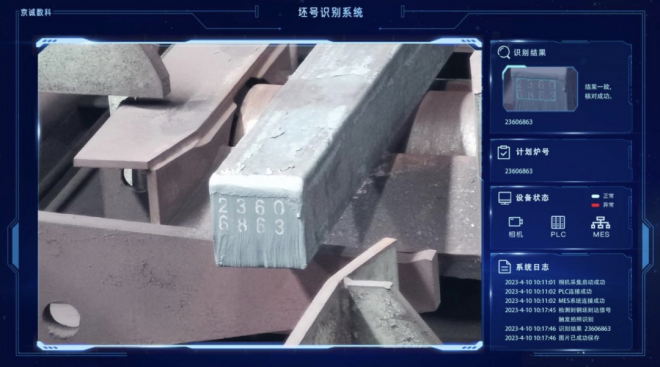
?。?)彎鋼/脫方/測長檢測系統(tǒng)
通過機器視覺識別方法,計算待入爐鋼坯長度方向兩個維度的彎曲率、斷面形狀和尺寸、鋼坯長度,如果出現(xiàn)彎鋼、脫方、超長情況,及時進行報警,并與PLC控制系統(tǒng)聯(lián)動,實現(xiàn)異常坯料的自動剔除,避免不合格鋼坯進入加熱爐。其中當鋼坯彎曲度每米大于20mm,總彎曲度大于總長度2%時的檢出正確率大于99%,系統(tǒng)可有效代替爐前看鋼人員進行彎鋼、脫方和長度檢測,顯著降低工人勞動強度,避免生產(chǎn)事故。
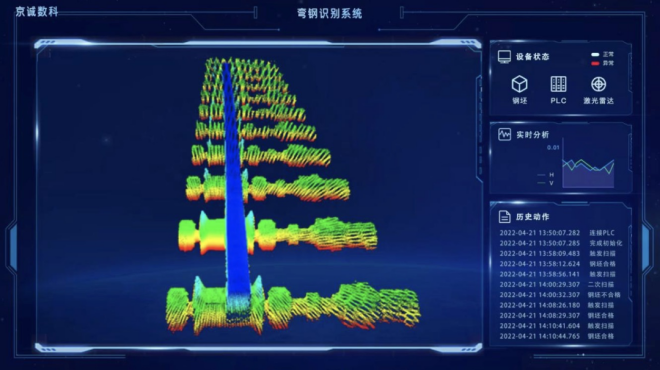
?。?)打滑檢測系統(tǒng)
在長材生產(chǎn)過程中,鋼坯在粗軋咬入時打滑現(xiàn)象偶有發(fā)生,且隨著生產(chǎn)集控的推廣,發(fā)生鋼坯打滑時,操作員難以及時發(fā)現(xiàn)并處理。系統(tǒng)采用工業(yè)相機對粗軋入口區(qū)域進行監(jiān)控,并基于自主開發(fā)的算法對鋼坯的咬鋼圖像幀進行實時分析,快速檢測出鋼坯打滑情況,并及時通知生產(chǎn)人員進行干預,顯著降低操作人員的工作強度,提高異常處理的及時性。
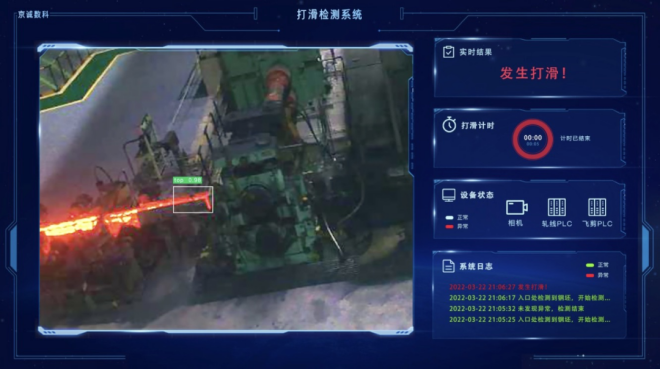
?。?)堆鋼檢測系統(tǒng)
當長材生產(chǎn)發(fā)生堆鋼事故時,尤其在發(fā)生飛鋼時將需要停機進行處理,嚴重影響生產(chǎn)作業(yè)率。系統(tǒng)采用工業(yè)相機對機架區(qū)域和活套進行監(jiān)控,并基于自主開發(fā)的算法對軋機間及其前后區(qū)域和活套的圖像幀進行實時分析,并結(jié)合自主開發(fā)的產(chǎn)線預警診斷專家系統(tǒng),實現(xiàn)堆鋼預警和堆鋼報警,并與PLC控制系統(tǒng)進行聯(lián)動,當系統(tǒng)判斷出堆鋼趨勢后,由飛剪啟動碎斷,避免發(fā)生事故,顯著提高生產(chǎn)作業(yè)率。
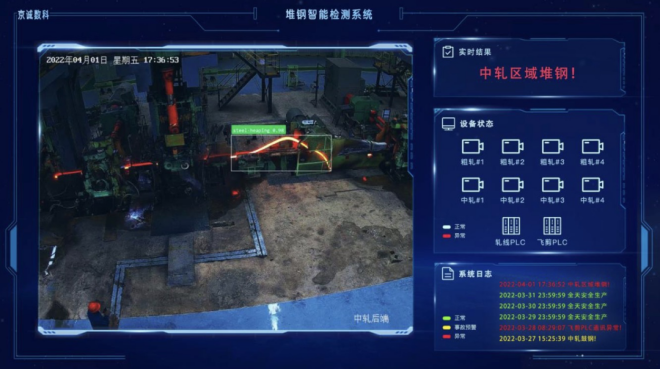
?。?)棒材定尺擋板對齊識別系統(tǒng)
棒材生產(chǎn)過程中,在定尺擋板撞齊的工藝位置,由于無法進行實時自動地對齊狀態(tài)檢測,導致剪區(qū)無法實現(xiàn)全自動運行,必須依靠人工目測和現(xiàn)場指揮。系統(tǒng)通過機器視覺+AI的方式實時檢測棒材的對齊狀態(tài),確認是否完成對齊,并將識別結(jié)果實時傳送給PLC控制系統(tǒng),實現(xiàn)對倍尺來料的自動剪切,提高剪切線生產(chǎn)節(jié)奏,降低由于頭部未對齊剪切導致的短尺問題,解決了制約該工藝段自動化生產(chǎn)的瓶頸問題。
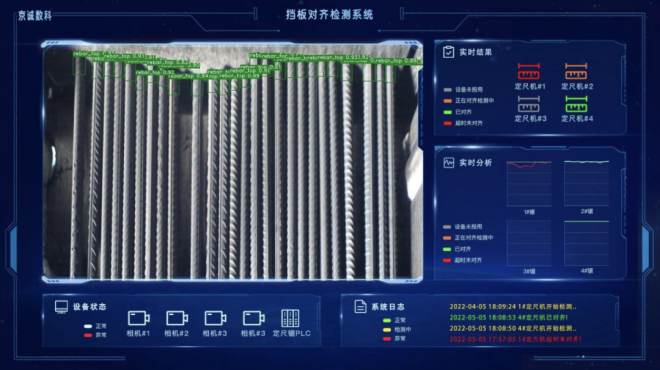
?。?)棒材收集區(qū)視覺跟蹤
棒材收集區(qū)由于成品數(shù)量多、檢測元器件不穩(wěn)定、人工干預多等原因,往往很難做到準確的全自動物料跟蹤。系統(tǒng)通過深度學習+AI算法,動態(tài)識別軋件在臺架上的位置坐標,并與過程控制系統(tǒng)相結(jié)合,準確跟蹤精整區(qū)棒材物料,為實現(xiàn)精整區(qū)不同子系統(tǒng)之間的全自動集成(如自動噴號、自動掛牌、自動分鋼等)、嚴格的混鋼控制、自動或無人稱重等應用提供了基本保障。
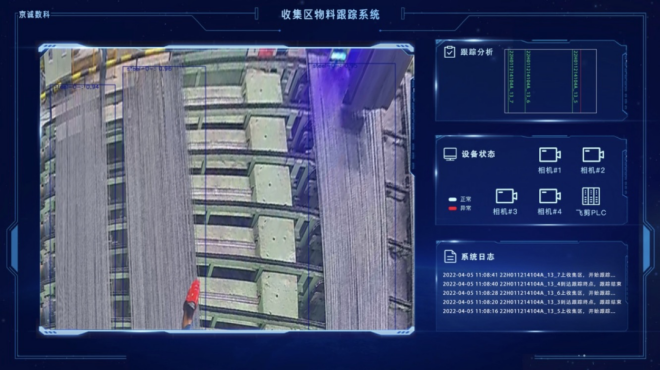
(7)C型鉤識別
采用深度學習的方式實現(xiàn)C型鉤號碼的識別,有助于實現(xiàn)全流程物料跟蹤,實現(xiàn)生產(chǎn)物流信息的準確追溯,減少人員的手工確認和操作頻繁度。系統(tǒng)可識別標準噴印體及手寫體,同時支持變角度識別,對于符合規(guī)范的字體識別準確率可達100%。
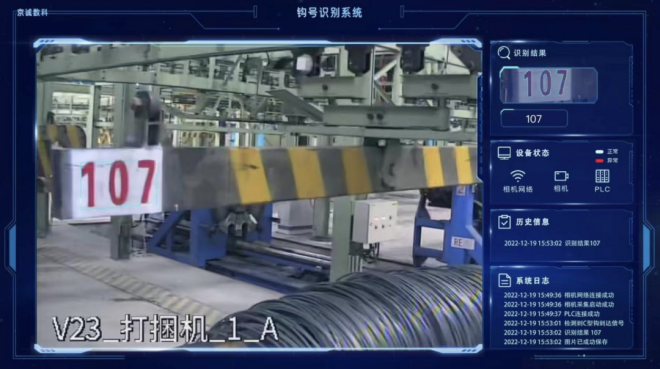
提質(zhì)增效成果顯著
中冶京誠機器視覺智慧感知平臺投用后,準確銜接煉鋼與軋鋼數(shù)據(jù),真正實現(xiàn)了生產(chǎn)按支跟蹤管理和質(zhì)量按支追溯;大幅降低崗位人員的勞動強度,提高操作及時性和準確率;精簡相應崗位人員,同時,解決傳統(tǒng)條件影響作業(yè)率提升和故障控制的瓶頸因素,從特定場景進行產(chǎn)能挖掘,大幅降低生產(chǎn)成本;提高了產(chǎn)線的智能化水平,通過機器視覺+AI的應用,可實現(xiàn)實時檢測、智能預警、即時報警、輔助控制等,在產(chǎn)線定員不變或定員精簡的情況下,人員的工作效率更高和產(chǎn)線控制更優(yōu),實現(xiàn)減員增效,為打造智能車間提供了技術(shù)保證。
此外,中冶京誠數(shù)科公司已成功將機器視覺智慧感知平臺在厚板車間以及智能天車等諸多應用場景中使用,未來將持續(xù)聚焦行業(yè)智能化技術(shù)研發(fā)攻關(guān),為鋼鐵企業(yè)數(shù)字化、智能化發(fā)展做出卓越貢獻。