在鋼鐵行業(yè)邁向綠色轉型的關鍵時期,氮氧化物(NOx)的超低排放治理與碳減排雙重挑戰(zhàn)亟待破局。傳統(tǒng)SCR脫硝技術雖能實現(xiàn)超低排放,卻因需將煙氣加熱至280℃左右運行,導致能耗與碳排放居高不下的矛盾成為制約行業(yè)綠色發(fā)展的核心痛點。在此背景下,中冶京誠工程技術有限公司(以下簡稱“中冶京誠”)技術團隊歷時多年潛心研發(fā)出超低溫SCR脫硝技術,為行業(yè)發(fā)展帶來新希望。該技術創(chuàng)造性地采用新型催化劑體系,在120-140℃區(qū)間即可實現(xiàn)90%以上的脫硝效率,相比傳統(tǒng)工藝,降低運行溫度160℃,無需額外加熱,便能高效凈化煙氣,可消減30-40%的年度運行成本,切實達成“減污降碳”目標,高度契合鋼鐵行業(yè)節(jié)能減排需求,極具推廣價值。
攻克技術難題
開拓低溫脫硝新方向
鋼鐵行業(yè)規(guī)模龐大,是典型的高能耗高排放行業(yè),對低能耗的“減污降碳”技術需求迫切。目前最有效的脫硝技術仍是氨氣選擇性催化還原(NH?-SCR)技術,而NH-SCR脫硝技術中最關鍵的就是脫硝催化劑?,F(xiàn)有的釩鎢鈦(V?O?-WO?(MoO?)/TiO?)脫硝催化劑體系一般在280℃左右穩(wěn)定高效,但這類催化劑需先借助換熱器對原煙氣升溫,再消耗大量煤氣升溫30℃及以上,成本高昂且碳排放量大增,以一臺360㎡的燒結機為例,每年因加熱煙氣額外增加2500萬的運行成本和近7萬多噸的CO?排放。因此,想要更徹底地實現(xiàn)減污降碳、降本增效,研發(fā)高效低溫脫硝催化劑勢在必得。
中冶京誠研發(fā)的無熱源式超低溫SCR脫硝技術,精準回應行業(yè)需求。在無需額外熱源下實現(xiàn)低溫脫硝,既降成本又減排放,是助力鋼鐵企業(yè)憑借綠色優(yōu)勢參與市場競爭的前沿技術。
突破關鍵瓶頸
研發(fā)新型催化劑
盡管不少低溫脫硝催化劑材料在實驗室尺度的驗證上表現(xiàn)出優(yōu)異的反應性能,但實際應用中仍存在抗中毒性能差的技術瓶頸。部分研究通過在傳統(tǒng)的釩鎢鈦脫硝催化劑體系引入等離子體技術進行輔助脫硝,卻增加了額外的設備投資和更多能耗,國內(nèi)穩(wěn)定且低成本的超低溫脫硝技術尚屬空白。
中冶京誠聚焦鋼鐵行業(yè)煙氣低溫脫硝技術,全力攻關,突破現(xiàn)有低溫催化劑存在低溫活性差、抗硫中毒性能差、抗堿金屬中毒性能差等關鍵技術瓶頸,開發(fā)出新型催化劑材料,并優(yōu)化催化劑配方,提升SCR催化脫硝效率,降低制備成本,成功研制新型超低溫SCR脫硝催化劑,為該技術的廣泛應用筑牢基礎。一旦該技術大規(guī)模推廣,將在鋼鐵行業(yè)引發(fā)綠色變革,提升環(huán)保與經(jīng)濟效益。
中試成果顯著
引領行業(yè)能效革新
中冶京誠歷時多年開發(fā)新型低溫SCR催化劑,其表現(xiàn)出優(yōu)異的低溫脫硝活性、抗硫性能和抗堿金屬中毒性能,且活性組分不易脫落,物理機械性能優(yōu)良。基于此,中冶京誠設計、建成鋼鐵行業(yè)首個超低溫SCR脫硝技術中試裝置。
中試項目已投產(chǎn),經(jīng)過3個月連續(xù)運行,NOx脫除率在120-140℃可達在90%以上,出口NOx<50mg/Nm3,滿足超低排放要求。試驗直接抽取的在運行鋼廠的燒結機脫硫出口煙氣,顛覆性地在不需要額外加熱的保溫煙氣條件下實現(xiàn)了高效脫硝。與傳統(tǒng)技術相比,脫硝溫度降低約160℃,無需消耗燃氣進行額外補熱升溫,運行費用下降了約30-40%,在實現(xiàn)超低排放的同時,節(jié)省燃氣資源,減少碳排放,創(chuàng)造極致能效,為推廣全新的超低溫脫硝技術提供了有力的支撐。
踐行“雙碳”理念
推動行業(yè)綠色發(fā)展
中冶京誠該項目貫徹落實國家“雙碳”重大戰(zhàn)略決策,推進鋼鐵行業(yè)環(huán)保降碳技術創(chuàng)新。通過對超低溫SCR脫硝工業(yè)試驗進行能耗、碳減排和技術經(jīng)濟性評價,全面驗證催化劑與設備的實用性,推動該技術大規(guī)模工業(yè)應用,為鋼鐵行業(yè)綠色低碳發(fā)展探索有效途徑。
展望未來,中冶京誠將秉持創(chuàng)新驅(qū)動發(fā)展戰(zhàn)略,深耕鋼鐵行業(yè)環(huán)保降碳領域,踐行“減污降碳”理念,探索冶金行業(yè)節(jié)能減排新方向,聚焦研發(fā)高附加值新材料、優(yōu)化催化劑配方等,為鋼鐵行業(yè)綠色轉型、極致能效的商業(yè)化實施持續(xù)發(fā)展貢獻力量。
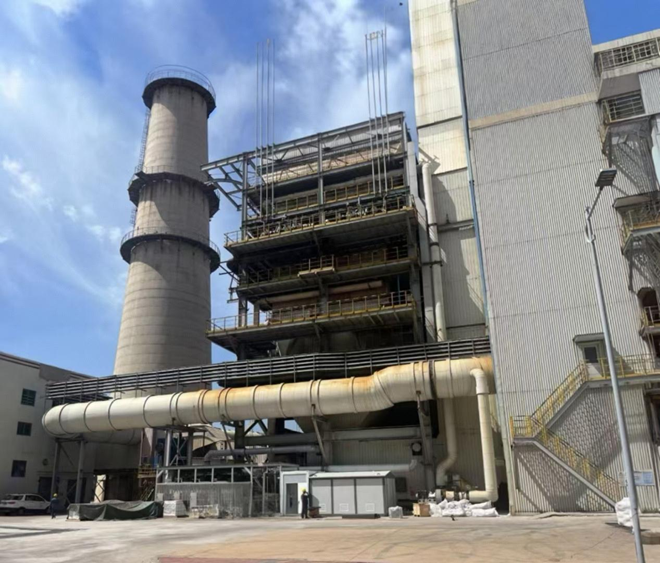